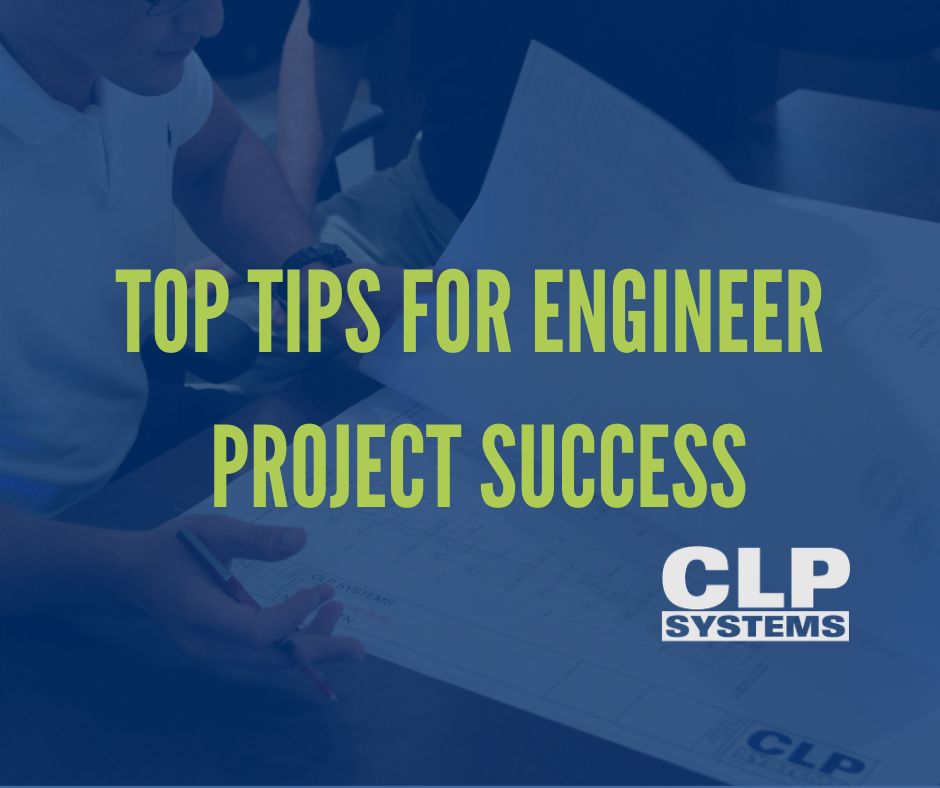
Wood frame engineers, did you know taking a few steps early in the project can help you design easier, build better, and set your projects up for long-term structural success? We asked our team what the best tips are they could share when it comes to ensuring the tie-down scope runs successfully. Here are their top tips to guide you:
- Design anchors in accordance with the Anchoring to Concrete chapter in the ACI 316, or note “anchors to be designed by hold-down supplier” on the shear wall schedule or anchor detail. The capacities provided in a manufacturer’s catalogue require certain criteria, like edge distance and concrete thickness, that are not typical scenarios. Be advised that cast-in-place anchors on slab-on-grade foundations are difficult to locate during the concrete pour. It is recommended to use embed plates for higher loads, and post-installed epoxy anchors for smaller loads at SOG foundations. Cast-in-place anchors are feasible for an elevated slab but embed plates may still be needed for higher loads. Also, if the engineer of record defers anchor design to the hold-down designer, it is recommended to include a note that concrete requirements need to be provided by the hold-down designer prior to setting concrete.
- Design compression stud packs using the NDS requirements or note “compression posts to be designed by hold-down supplier” on the shear wall schedule or hold-down detail. Keep in mind that the minimum wood member thickness in a manufacturer’s catalogue for conventional hardware is the minimum thickness for connection purposes only; story height and wood strength still need to be evaluated to determine the compression post size. Compression due to the overturning moment is assumed to be equal and opposite of the tension force in the rod according to Section 4.3.6 of the Special Design Provisions for Wind & Seismic (AF&PA SDPWS). If the hold down supplier is to design the compression posts, then the engineer of record should provide compression loads if they are not equal to the tension loads. Compression studs should be located at a maximum distance on both sides of the rod. If the bearing plates are on a double top plate, the maximum distance should be 3” to fall within the 45-degree bearing zone. Plate bending and shear needs to be investigated if the studs do not fall within the bearing zone.
- Shrinkage must be accounted for any building supporting more than two floors and a roof according to the IBC. The AC 316 provides a conservative limit for total shrinkage compensating device deflection and rod elongation of 0.2” per floor, unless the engineer of records drift analysis allows for more movement, therefore the plans should specify deflection and elongation requirements or include a note to follow AC 316 requirements. A detail should also be included in the structural plans to visually show a shrinkage compensating device to ensure the requirement is not missed during estimating. This will also ensure that bids stay competitive among suppliers while maintaining structural quality.
- Bearing plates and shrinkage compensating devices are designed for incremental loads on each floor. The bearing capacity needs to be equal to or greater than the load at the floor below minus the load at the floor of the bearing plate.
CLP wants to help guide you to have the project success you want! If you are interested in having the most successful project you have ever had, call us at 800-214-7673 to get started today.