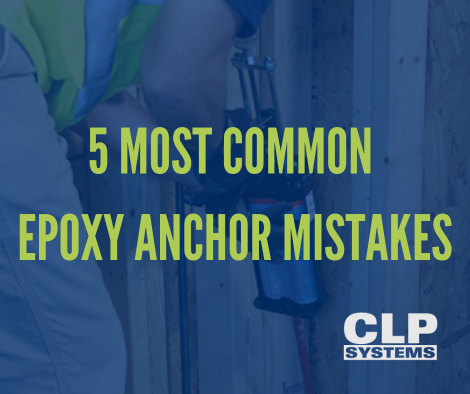
In today’s market, many general contractors shy away from cast-in-place and embed plate anchoring solutions due to the cost and time it takes to install. These anchoring solutions can cause many frustrations on wood frame projects that delay construction timelines.
To overcome these installation variables, general contractors and framers have increasingly looked to drill and epoxy solutions to help expedite project timelines and mitigate anchor issues. Epoxy anchoring is cheaper, easier, and quicker to install making it a popular choice for install crews.
But, is it comparable in strength and a viable alternative?
For lower tensile demands, the short answer is yes, but installation variables can quickly diminish the structural integrity of epoxy anchors. If not installed and cured properly, then the epoxy will no longer maintain the required load value to ensure structural integrity of the anchor. Below are the 5 most common mistakes while installing epoxy:
1.Incorrect Drill Depth and Size – Every anchor has a required embedment depth and diameter that contribute to its capacity within the concrete foundation. It’s common for installers to not drill deep enough to achieve the required embedment depth. Taking the time to measure and accurately drill the hole is the first step in guaranteeing the anchor will maintain its required value.
2.Not Properly Cleaned – Concrete dust and small trash can easily prevent the full embedment depth of the anchor, and mix with the epoxy, reducing the curing strength of the epoxy. It is important to make sure each hole is brushed and cleaned according to manufacturer specifications before installing the anchor. Failing to do so puts the structural integrity of the project at risk.
3.Standing Water in the Hole – It’s common to see standing water on job-sites. Whether it’s caused by natural rain or from clean-up crews, it can easily fill or partially fill a drilled hole. It is required that the concrete hole is dry before epoxy installation. All water should be removed from the hole using a vacuum and/or compressed air prior to cleaning.
4.Temperature Too Cold – Ambient temperatures can have negative effects on the proper curing of epoxy. When installing an epoxy anchor, manufacturers require that the temperature of both the concrete and the epoxy are within their allowable installation temperature range. It’s important to maintain these temperatures range. To solve this issue, it is good practice to keep epoxy stored inside a job site trailer or under controlled temperature at all times.
5.Incorrect Curing Times – Adhesive curing times can vary from 4 and 48 hours and more, so it’s important to not disturb, torque, or load the anchor until the epoxy has fully cured. It’s common for installers to assume epoxy curing times so it’s important to check curing time tables for manufacturer’s recommendations in order to accurately prepare project timelines.
These common mistakes are critical to the curing strength of epoxy. At CLP Systems, we work closely with our customers and engineers to design the best solutions that meet and exceed industry expectations. In the past 18 years, CLP Systems has helped engineers, general contractors, and framers on more than 4,000 multi-family wood frame structures. Understanding anchor issues and design needs of our customers, the CLP team not only focuses on providing the best products but also providing comprehensive project management and quality service to ensure our solutions are designed and installed correctly.